Blog
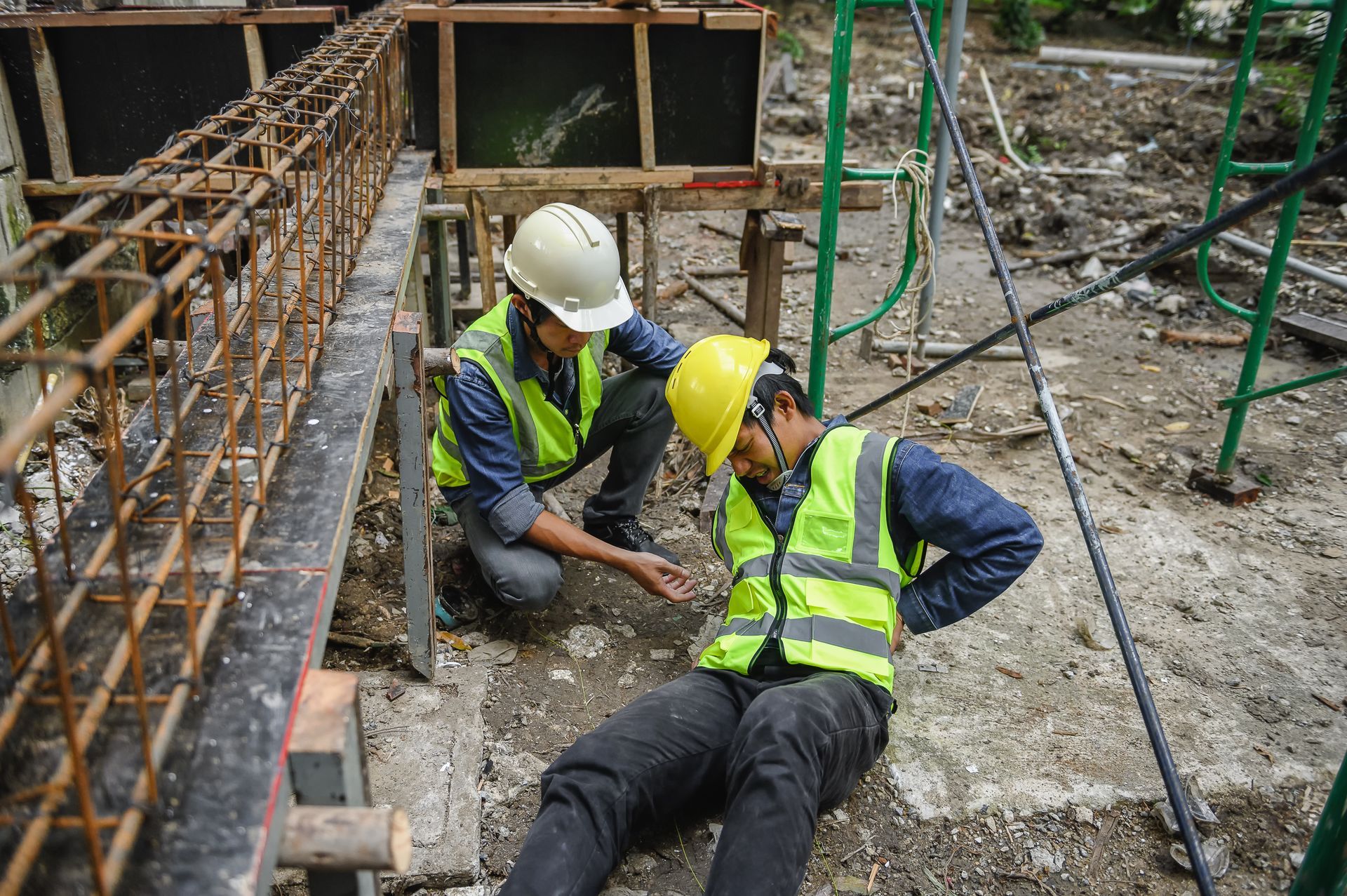
In the construction industry, where the nature of the work often involves hazardous conditions, the risk of site accidents is a constant concern. For construction companies, these accidents can lead to costly claims and legal battles, damaging both financial stability and reputation.
However, with rigorous safety training, strict enforcement of safety rules and diligent maintenance of equipment, companies can significantly reduce the risk of accidents and strengthen their defense against potential claims.
Safety Training: The Foundation of Accident Prevention
Effective safety training is the cornerstone of accident prevention on construction sites. Making sure that all employees are well-versed in safety protocols and procedures not only helps in preventing accidents but also demonstrates a company’s commitment to maintaining a safe work environment.
1. Comprehensive Safety Orientation
- Initial Training: Every new hire should undergo a thorough safety orientation that covers the basics of construction site safety, including the use of personal protective equipment (PPE), hazard recognition and emergency procedures.
- Role-Specific Training: Tailor safety training to specific roles within the company. For example, scaffolders should receive specialized training in scaffold safety, while heavy machinery operators should be trained in the safe operation of their equipment.
2. Continuous Education
- Regular Safety Meetings: Conduct regular safety meetings to keep safety at the forefront of employees’ minds. Use these meetings to review recent incidents, discuss new safety protocols and address any concerns.
- Ongoing Training Programs: Implement ongoing training programs that strengthen risk mitigation practices and provide guidance on new safety regulations and techniques. This continuous education helps to reinforce safety practices and makes it more likely employees will remain vigilant.
Enforcing Safety Rules: Building a Culture of Safety
Creating a culture of safety within a construction company requires more than just training; it involves the consistent enforcement of safety rules and protocols.
Clear Safety Policies
Develop clear, comprehensive safety policies that outline expectations for behavior and procedures on the job site. Confirm that these policies are easily accessible to all employees. Regularly communicate safety policies and updates to all staff. This can be done through meetings, newsletters or posted notices on the job site.
Accountability
Conduct regular safety audits to confirm company-wide compliance with safety rules. Use these audits to identify areas for improvement and implement corrective actions as needed. Establish a system of consequences for failing to adhere to safety rules. This could range from additional training sessions to disciplinary actions, depending on the severity of the infraction.
Leadership Commitment
Encourage leaders and supervisors to model safe behavior. When management demonstrates a commitment to safety, it sets a standard for the entire workforce. Consider implementing safety incentive programs that reward employees for safe behavior and adherence to safety protocols. This can motivate employees to prioritize safety in their daily tasks.
Ensuring Equipment is in Good Working Order
The proper maintenance of equipment is crucial in preventing accidents on construction sites. Faulty or poorly maintained equipment can pose significant risks to workers, leading to accidents and subsequent workers’ comp or third-party claims.
Regular Inspections
- Daily Checks: Require daily inspections of all equipment before use. Operators should check for any signs of wear and tear, malfunction or equipment-specific hazards that could pose a safety risk.
- Scheduled Maintenance: Implement a schedule for regular maintenance of all equipment. This should include routine servicing, part replacements and any necessary repairs.
Maintenance Logs
Keep detailed maintenance logs for all equipment. These logs should document inspections, maintenance activities and any repairs performed. This not only helps in tracking the condition of equipment but also serves as evidence of diligent maintenance in the event of a claim.
Training for Equipment Operators
All equipment operators must be trained in the proper use of their machinery. This includes understanding the manufacturer’s instructions, operating within safe limits and recognizing when equipment needs maintenance.
Train operators in emergency procedures related to equipment failure. Knowing how to respond in case of an equipment malfunction can prevent accidents and reduce the severity of incidents.
Building a Robust Defense Against Claims
Despite the best preventive measures, accidents can still occur. When they do, having a robust defense strategy is essential for construction companies to protect themselves from claims.
Incident Investigation
- Thorough Investigations: Conduct thorough investigations of all incidents to determine the root cause. This involves interviewing witnesses, reviewing maintenance logs and analyzing the sequence of events leading to the accident.
- Objective Reporting: Maintain objective and detailed incident reports that document the findings of the investigation. These reports can be crucial in defending against claims by providing evidence of compliance with safety protocols.
Experienced Construction Site Liability Defense Lawyers in Atlanta
When facing a construction site liability claim, having the right commercial liability defense lawyer is a necessity. The Law Office of Cameron Hawkins in Atlanta, GA is equipped to defend construction companies against accident claims.
Don't leave your company's future to chance. Contact us at the Law Office of Cameron Hawkins online for a free consultation or give us a call at 678-921-4225.